Products
Key Functionality & Technical Papers
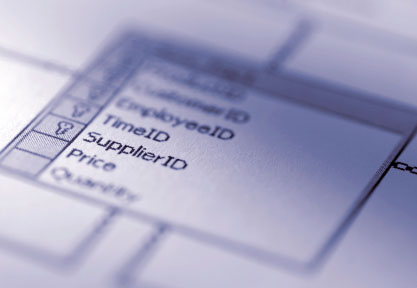
Lean Six Sigma
1. What is Six Sigma?
In today's business world this has more meaning than just a failure rate. It is a methodology that is being adopted by enterprises to increase their profitability through improving the Sigma capability of their business processes. In essence, Six Sigma means overall excellence, not only in the finished product, but also in the administrative, service, and the business processes throughout the whole organization.
"Six Sigma" (taken from a letter in the Greek alphabet) literally means a failure rate of 3.4 per million.
2. The Methodology
The Six Sigma methodology is a structured approach. It consists of five core phases namely Define, Measure, Analyze, Improve, and Control (DMAIC) that allow companies to make exceptional bottom-line improvements.
- 2.1 Define
- The Define phase is a thorough assessment of the current business environment. This primarily includes understating an organization's strategic and operational objectives. In detail this phase entails understanding the customer and their needs, developing a charter, identifying key metrics, etc.
- 2.2 Measure
- The Measure phase includes a review of the types of measurement systems and their key features, as well as the frequency with which defects occur and the process capability, which governs the creation of defects. Establishing valid and reliable metrics to help monitor progress towards the enterprise goal is also a key part of the measure phase. Exploratory and descriptive data analysis techniques are used to help understand this data. At the top level the goals will be the strategic objectives of the organization, such as a higher ROI or market share. At the operations level, a goal might be to increase the throughput of a production department. At the project level goals might be to reduce the defect level and increase throughput.
- 2.3 Analyze
- The Analyze phase uses specific statistical methods and tools to isolate key pieces of information, which are critical to the number of defective products. In this phase, practical business problems are turned into statistical problems. The system is analyzed to identify ways to eliminate the gap between the current performance of the system or process and the desired goal.
- 2.4 Improvement
- The Improve phase focuses on discovering the key variables, which cause the problem. The key is to improve the existing system. This can be achieved by finding new ways to do things better, cheaper, or faster. Project management and other planning and management tools are used to implement the new approach. Statistical methods are used to validate the improvement.
- 2.5 Control
- The Control phase ensures that the same problems don't reoccur by continually monitoring the processes that create the product or service. Modifying compensation and incentive systems, policies, procedures, MRP, budgets, operating instructions and other management systems, may institutionalize the improved system.
3. Discrete Event Simulation with SIMPROCESS
Design of Experiments (DOE) - a statistical approach, determines the number of experiments to conduct in order to gather the optimal level of process performance data that then can be used to identify variables and variable relationships that exert the greatest influence on system characteristics.
Many organizations are finding that they are limited in their ability to conduct the required experiments. Conducting tests in the field could:
- Result in costly manufacturing line downtime
- Result in excessive scrap
- Result in measurements not taken often enough for valid analysis
- Result in costly resource downtime
- Result in testing a flawed hypotheses which translates to a wasted effort
- Mean conducting fewer than the optimal number of tests
- Be too time consuming
However, SIMPROCESS is a tool for creating system models and executing them as discrete-event simulations. Discrete-event simulation models represent systems from an object-oriented perspective, i.e., the modeler can focus on defining and interconnecting system components and let the tool resolve the complexities of inter-component behavior. This capability facilitates modeling of very complex systems where analytical modeling techniques would be unrealistic.
SIMPROCESS provides a detailed view of the system design and facilitates identification of scenarios where the system may "lock-up." SIMPROCESS models can have a highly detailed representation of system design and logic. The SIMPROCESS model can assess the performance of system designs under realistic loading conditions to determine if design flaws surface under increased event rates and volumes.
4. SIMPROCESS Augments Six Sigma
The use of SIMPROCESS augments and strengthens a phase-by-phase Six Sigma implementation. Overall benefits include reduced experimentation duration and costs through simulation, reduced costly field implementations of incorrect solution through solution validation, and reduced measurement time with an easy-to-use tool.
- 4.1 Define
- SIMPROCESS will support an organization:
- Assess current business environment.
- Develop a framework that mimics the current business environment.
- Provide a start point for measurement & analysis of organizational and operational performance.
- 4.2 Measure
- SIMPROCESS will support an organization:
- Capture and organize more comprehensive process data, reduce the overall measurement cost and time, and establish a framework used throughout the Six Sigma life cycle.
- Uncover process inefficiencies (bottlenecks) and non-value added activities (NVA).
- Identify key factors and variables influencing the business process performance.
- 4.3 Analyze
- SIMPROCESS will support an organization:
- Benchmark internal processes and industry best practices.
- Provide the most cost-effective, accurate, and rapid strategic weapon for businesses to evaluate alternatives prior to implementing them.
- Visualize how a process would behave, measure its performance, and try "what-if" scenarios. It provides an animated picture of the flow and real time graphs of concerned performance measures. Also contains a comprehensive set of statistical tools. This suite of tools can be used to fit input data to a distribution, to design and run experiments, and to analyze the results from multiple simulation run.
- 4.4 Improvement
- SIMPROCESS will support an organization:
- Eliminate all potential pitfalls by conducting experiments through the power of simulation.
- Create alternative representations of a business process within the same model. Use of Scenario Manager would compare the alternatives, and help in choosing the one that maximizes service levels and profits ("to be").
- Generate concise reports of results. In addition to the "standard report", custom reports can be generated for keeping track of service levels, in-process inventory, and makespan. All reports can be viewed in tabular or graphical form and printed or exported to other software packages.
- 4.5 Control
- SIMPROCESS will support an organization:
- Enable rapid mapping of the improved process.
- Seamlessly interface between with other object-oriented workflow management and application development tools.
- Provide an integrated solution for continuous process improvement (CPI).
- Monitor and control improved processes through the use of real time plots, bar charts, histograms and more. Charts can be easily viewed using MS Office.
5. What You'll Finally See
Integrating process mapping, object-oriented simulation, and activity-based costing into a single tool, SIMPROCESS meets the most demanding needs for a Six Sigma implementation and its concerned maintenance.
An enterprise engaged in a Six Sigma implementation augmented with SIMPROCESS can expect to see:
- Improved customer satisfaction
- Reduced cycle times
- Increased productivity
- Improved capacity and output
- Reduction in total defects
- Increased product reliabilitys
- Decreased work-in-progress (WIP)
- Improved process flow